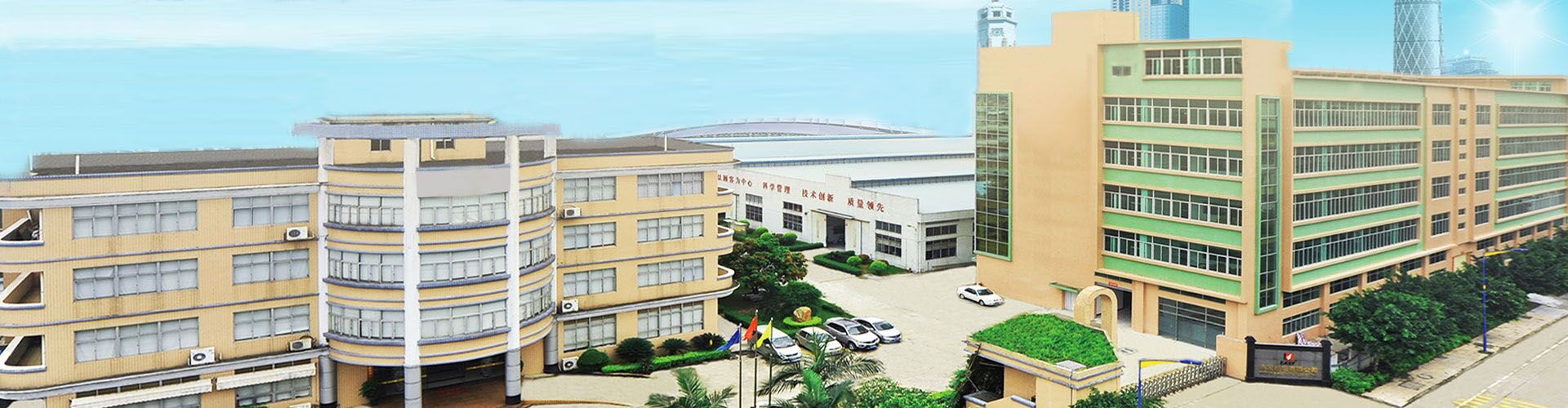
Join TMAX, become an agent!
Sales Manager:David
Email:David@tmaxcn.com
Wechat:18659217588
Item No.:
TMAX-YK-800*750-LPayment:
L/C, T/T, Western Union, Credit Cards, PaypalProduct origin:
ChinaShipping port:
Xiamen PortLead Time:
5 DaysCertificate:
CE, IOS, ROHS, SGS, UL CertificateWarranty:
Two years limited warranty with lifetime technical support
1、List of equipment specifications
No. |
Equipment name |
Equipment model |
Remarks |
1 |
High Precision Lithium Battery Rolling Press Machine |
TMAX-YK-800*750-L |
The effective rolling width is 200~680mm. |
1.1 Equipment composition and function
Main configuration of equipment
No. |
Name |
Place of Origin |
1. |
Air switch |
Schneider (France) |
2. |
PLC |
Siemens (Germany) |
3. |
Touch screen |
Smet (Taiwan) |
4 |
Modular |
Siemens (Germany) |
5. |
Intermediate relay |
Schneider (France) |
6. |
Drive servo motor |
Siemens (Germany) |
7 |
Reducer |
International Trade (China) |
8. |
Memorial Gateway |
Shaogang (China) |
9. |
Bearing |
Wafangdian (China) |
10. |
Coupling |
Zhengtong (China) |
11 |
Hydraulic ram cylinder |
Siemark (Germany) |
12. |
Full automatic tension |
PID closed loop control (self-made) |
13. |
Deep groove ball bearing (machine head) |
NSK (Japan) |
14. |
Frequency converter |
Rexroth (China) |
15. |
Rectify deviation |
Dongdeng (Guangzhou) |
2、Introduction to equipment principle
The traction of electrode is compacted to the predetermined thickness or the predetermined compaction density by the double action of pressure and the nip of the pressure roller, so that the lithium battery produced by the rolled pole piece can achieve the designed / predetermined volume energy density and battery performance.
No. |
Project |
Describe |
Note |
1 |
Suitable system |
Continuous rolling process for positive and negative plates of lithium iron phosphate, lithium cobalt oxide, lithium manganate, lithium nickel cobalt manganese and other battery systems. |
|
2 |
Rolled substrate |
Aluminum foil (10um-1.5mm), copper foil (6um-1.5mm), |
|
3 |
Rolling mode |
Width: 200mm-750mm. |
Motor drive position |
4 |
working pressure |
The two rollers are rolled up and down horizontally, and the drive is located on the right side of the feeding end. |
|
5 |
Equipment speed |
Provided by constant pressure pump station, it is suitable for positive high pressure rolling and negative low pressure adjustment. |
|
6 |
control mode |
Stepless adjustment, and the linear speed of the upper and lower rollers is equal. |
|
3、Equipment action sequence
Technological process of counter roll (pole rolling)
4. Equipment composition and functional
Equipment component configuration
4.1 unwinding system (as shown in Figure 1)
Figure 1
No. |
Project |
Describe |
Note |
1 |
Discharging part |
φ 76mmx750mm inflatable shaft unwinding, equipped with air gun |
|
2 |
Receiving platform |
Pneumatic lifting of steel plate front receiving platform and pressing plate |
|
3 |
tension control |
Swing roll type, low friction cylinder controls the tension, and the sensor detects and displays the tension |
|
4 |
Deviation correction system |
Photoelectric deviation correction and linear guide rail (the maximum moving range is 100mm) |
|
5 |
Rectification execution |
Dongdeng deviation correction actuator |
|
6 |
Sub control system |
The discharging and receiving end is equipped with equipment sub control system and emergency stop (dynamic brake), pause and other buttons |
|
7 |
Iron removal before rolling |
Electromagnetic pole piece iron removal device, magnetic force of magnetic rod 10000~12000 Gauss |
|
Figure 2
No. |
Item |
Describe |
Remarks |
1 |
Knife feeding requirements |
Pneumatic slitting blade (HRC ≥ 58). |
|
2 |
Cutting requirements |
¢ 150*50 bottom knife. |
|
3 |
Trimming speed |
It can automatically match the rolling mill running line speed (i.e. synchronization, response time ≤ 10ms), and |
|
4 |
Scrap recycling |
Can be adjusted separately; There is no material dropping and broken belt at the cutting edge. |
|
5 |
Trimming width |
Automatic collection, equipped with receiving box. |
|
4.3 Dust removal system before pole pressing (as shown in Figure 3)
Figure 3
No. |
Item |
Describe |
Remarks |
1 |
Vacuum suction |
Reserve the interface of industrial vacuum cleaner. |
|
2 |
Brush cleaning |
The pneumatic lifting upper box is in contact with the rolling brush mode. The dust on the material belt is cleaned by the brush, and the dust is sucked away by the vacuum cleaner. |
|
3 |
Iron removal before rolling |
Electromagnetic iron removal device before pole rolling, with magnetic force of 10000 ~ 12000 Gauss. The magnetic rod is placed in the stainless steel tube and is easy to be loaded and unloaded, and it is easy to remove the adsorbed iron. |
|
4.4.1Constant pressure high-precision battery pole piece rolling mill (as shown in Figure 4)
Figure 4
No. |
Project |
Description |
Note |
1 |
Roll installation |
The two rollers are arranged horizontally up and down, with an integral archway. |
|
2 |
dynamic system |
Dual motor torque dual output structure. |
|
3 |
Roll shafting |
Bearing clearance setting device, with oil lubrication device. |
|
4 |
Pole piece roller |
High alloy forged steel, double medium frequency induction quenching, electroslag remelting process. |
9Cr3mo |
5 |
Running speed |
0~30m/min, digital setting, stepless speed change, variable frequency speed control CNC system. |
|
6 |
working pressure |
Two hydraulic stations are used for pressurization. |
Online voltage regulation |
7 |
Roll gap adjustment |
0-2mm digital setting, automatic gap adjustment. |
The minimum unit of adjustment is 0.001mm |
8 |
Roll cleaning |
Automatic roller wiping |
|
9 |
Safety protection |
Stainless steel feeding hand guard is adopted. Equipped with emergency stop and pause. |
|
4.4.2 automatic roller wiping device (only negative pole, as shown in Figure 5)
Figure 5
Function Description: the non-woven fabric is wiped on the roll by moving, and the upper and lower rolls are wiped at the same time; Roller wiping speed can be adjusted; The pressure of non-woven fabric on the roll is adjustable.
4.5 Constant tension closed-loop winding system (as shown in Figure 6)
Figure 6
No. |
Project |
Describe |
Note |
1 |
Receiving part |
φ 76mmx750mm inflatable shaft unwinding, lock valve design, equipped with air gun |
|
2 |
Receiving platform |
Pneumatic lifting of steel plate front receiving platform and pressing plate |
|
3 |
tension control |
Swing roll type, low friction cylinder controls the tension, and the sensor detects and displays the tension |
|
4 |
Deviation correction system |
Photoelectric deviation correction and linear guide rail (the maximum moving range is 100mm) |
|
5 |
Deviation correction motor |
Dongdeng deviation correction actuator |
|
6 |
Winding power |
Winding motor (2.2kW) |
|
7 |
Iron removal after rolling |
Electromagnetic pole piece iron removal device, magnetic force of magnetic rod 10000~12000 Gauss |
|
4.6 PLC touch screen control system
No. |
Project |
Describe |
Note |
1 |
system composition |
Unwinding tension control, unwinding photoelectric deviation correction and deviation correction motor control, cutter motor control, rolling mill main drive control, constant pressure hydraulic station control, winding motor control, winding tension control, winding photoelectric deviation correction and deviation correction motor control |
|
2 |
Operation layout |
Control of braking, emergency stop and suspension. |
|
3 |
major function |
It is equipped with retraction and release sub control operation and main operation console, and all operation parts are equipped with emergency |
|
4 |
Auxiliary functions |
Stop and pause buttons (dynamic braking). |
|
5 |
safeguard |
It can digitally set the operation speed, pressure, gap between rolls and other instructions |
|
6 |
Counting function |
Full CNC operation of. |
|
4.7 Equipment installation requirements
4.7.1 power supply: 3Ph 380V, 50Hz, voltage fluctuation range: +8%~ – 8%; The total power of the power supply is 60KW plus a 10% safety factor.
4.7.2 compressed air: after drying, filtering and stabilizing: the outlet pressure is greater than 0.6~0.8mpa; Trachea is Φ 8。
4.7.3 ambient temperature: ≤ 28 ℃.
4.7.4 relative humidity: RH ≤ 85%.
4.7.5 ensure that the air on site is dry and unblocked without acid-base corrosion.
4.7.6 main engine installation foundation: the thickness of foundation cement in the main bearing area is not less than 40cm, and that in other areas is not less than 10cm; The main part of the equipment (battery pole rolling mill) needs to be installed on a concrete foundation with a ground bearing capacity of not less than 10T/m2.
5. Technical parameters
5.1 main process parameters
No. |
Project |
Describe |
Note |
1 |
Effective dimension of rolled surface |
Ф800mmx750mm, effective rolling width 200~680mm |
|
2 |
Line pressure between two rollers |
Max4000KN |
|
3 |
Non decaying hardness layer |
Min 19mm |
|
4 |
Roll hardness |
HRC≥67, hardness uniformity≤HS±2 |
Show the test report |
5 |
Roll surface roughness |
Ra≤0.2 |
Show the test report |
6 |
Roll straightness |
≤±0.0015mm |
|
7 |
Installed radial runout |
≤±0.0025mm |
|
8 |
Roll gap adjustable range |
0-2.0mm,digital setting adjustment accuracy 0.001mm. The left and right gaps between the two rollers are consistent |
|
9 |
Rolling accuracy |
≤±0.0015mm (Coating accuracy≤±0.003mm) |
|
10 |
Pressure control accuracy |
≤0.15T |
|
11 |
Equipment running speed |
Max30m/min |
|
12 |
Trimming width |
200mm-680mm |
|
13 |
Maximum diameter of winding and unwinding |
ф500mm |
|
14 |
Maximum width of reeling in and out |
680mm |
|
15 |
Maximum weight of reeling in and out |
500Kg |
|
16 |
Coil cylinder diameter |
Φ76mm |
|
17 |
Radial runout error of winding shaft during equipment operation |
≤±0.03 |
|
18
|
Roll surface of winding and unwinding shaft |
≤0.15 |
|
19 |
Roughness Ra |
≤±0.03 |
|
20 |
Coaxiality of winding shaft |
Max. 0.2mm |
|
21 |
Deviation correction accuracy |
0 ~ 50N adjustable |
|
22 |
Maximum tension of winding and unwinding |
Except for stainless steel, surface treatment and coated parts, the surface of other parts of the fuselage is coated with international computer white paint |
|
23 |
Device color |
(it can be sprayed according to the color card provided by the customer) |
|
24 |
Outline dimension |
About 3.9m × 1.8m × 1.8m × 2.9m (length × wide × High) |
|
25 |
Outline of rolling press machine production line |
About 28 tons |
|
26 |
Whole machine weight |
About 30 tons |
|
27 |
Main Power |
About 44KW |
|
6. Attached data and accessories
6.1 one copy of equipment operation manual, maintenance manual and relevant data, including equipment drawings, circuit and electrical diagrams of machines and main parts and accessories.
6.2 a list of vulnerable parts (indicating the model, material, supplier and other information of vulnerable parts, including the diagram of vulnerable parts).
No. |
Project |
Describe |
Note |
1 |
Composition of spare parts |
1 set of special maintenance tools |
|
2 |
Vulnerable parts |
1 set of hydraulic pipeline seal, 1 upper and 1 lower cutter, 2 scraper |
|
6.3 PLC program backup.
1 Standard exported package: Internal anticollision protection, external export wooden box packaging.
2 Shipping by express, by air, by sea according to customers' requirements to find the most suitable way.
3 Responsible for the damage during the shipping process, will change the damage part for you for free.
Previous :
Double Sides Slot Die Coating Machine for Prismatic Battery Electrode CoatingNext :
50000m3/H NMP Solvent Recovery System NMP Recycling SystemCategories
© Copyright: 2025 Xiamen Tmax Battery Equipments Limited All Rights Reserved.
IPv6 network supported