Powder Pellet Press Die: Essential Tool for Powder Compaction and Pellet Formation
A powder pellet press die is a crucial tool used in the manufacturing process of pellets from powders. It is typically employed in industries such as metallurgy, ceramics, pharmaceuticals, battery manufacturing, and chemical processing. The press die is designed to compact powdered materials into uniform, compact pellets, which can then be used for further processing, testing, or as final products.
Pellet presses are commonly used in applications where precise control over the pellet's density, size, and shape is required, as the quality of pellets plays a significant role in the subsequent processing or end-use performance.
● What is a Powder Pellet Press Die?
A powder pellet press die is a mold or cavity in a powder press machine that shapes powdered materials into pellets through high pressure. The die ensures the uniformity of size, shape, and density of the resulting pellets. These dies are made from high-strength materials that can withstand the extreme pressures involved in compacting powders into solid forms.
● Key Features of a Powder Pellet Press Die
1. Material Composition
- Typically made from high-grade steel, tungsten carbide, or other wear-resistant materials to ensure long-lasting durability and performance under pressure.
2. Customizable Sizes
- Pellet press dies can be custom-designed to create pellets of varying sizes, shapes, and densities. Dies are often interchangeable for different applications.
3. Multiple Cavities
- Some Lab Hot Press are designed with multiple cavities, allowing for the production of several pellets at once. This is especially important in high-throughput applications.
4. Precision Engineering
- High-precision manufacturing ensures that each die produces pellets of uniform size and weight, which is crucial for maintaining consistency in the final product.
5. Easy Maintenance
- Many modern press dies are designed for easy maintenance and cleaning to prevent contamination of different powders and ensure smooth operation.
● The Pellet Pressing Process
1. Powder Filling
- The powder to be compacted is placed in the die cavity. The powder can be a single material or a mixture, depending on the final pellet's requirements.
2. Compression
- The die is subjected to high pressure from the pellet press machine, causing the powder to compact into a solid form. The pressure causes the particles to bond together through mechanical interlocking, sometimes aided by a binding agent.
3. Pellet Ejection
- After compaction, the pellet is ejected from the die cavity, usually with the help of a punch or ejector mechanism.
4. Drying or Sintering (Optional)
- Depending on the material and application, the pellets may need additional processing, such as sintering or drying, to enhance their strength and stability.
● Types of Powder Pellet Press Dies
1. Single-Cavity Dies
- Designed to produce one pellet at a time, single-cavity dies are typically used for smaller-scale or high-precision applications where uniformity and high quality are critical.
2. Multi-Cavity Dies
- These dies have multiple cavities to produce several pellets simultaneously. Multi-cavity dies are used in high-volume applications where cost efficiency and speed are important.
3. Rotary Dies
- In rotary pellet presses, a rotating die mechanism allows for continuous pellet production, making them suitable for large-scale, continuous operations.
4. Custom Dies
- Custom pellet press dies can be designed for specific applications, including different shapes (such as cylindrical, spherical, or irregular), sizes, and materials.
● Materials Used in Powder Pellet Press Dies
The choice of material for a powder pellet press die depends on the specific requirements of the application, including the nature of the powder, pressure requirements, and wear resistance. Common materials include:
1. Tool Steel
- Used in applications requiring good durability and moderate resistance to wear.
2. Tungsten Carbide
- Known for its extreme hardness and resistance to wear, tungsten carbide is ideal for pressing highly abrasive materials.
3. Stainless Steel
- Corrosion-resistant and often used when working with powders that are chemically reactive or prone to oxidation.
4. Ceramic Materials
- For special applications, such as pressing ceramics or pharmaceuticals, die materials can include high-performance ceramics that can withstand high temperatures.
● Applications of Powder Pellet Press Dies
1. Battery Manufacturing (Li-ion, NiMH)
- In the production of electrodes for lithium-ion or nickel-metal hydride batteries, powder pellet press dies are used to compact materials such as graphite, nickel, and lithium into uniform pellets or electrodes.
2. Ceramics and Powder Metallurgy
- Pellet press dies are used to form ceramic pellets or metal powder pellets that will undergo sintering to form the final solid materials.
3. Pharmaceuticals
- Pharmaceutical powders are often pressed into tablets or pellets for ease of administration. Pellet press dies ensure consistent dosages and quality control.
4. Chemical and Fertilizer Production
- In the production of chemical pellets, including fertilizers, the press die forms uniform pellets that can be easily handled and processed.
5. Food and Animal Feed Production
- Pellet presses are also used in food and animal feed industries to produce pellets that are used for nutrition or processing.
● Benefits of Using Powder Pellet Press Dies
1. Uniformity and Consistency
- Pellets produced by a high-quality press die are uniform in size, shape, and density, which is critical for both industrial processes and final product performance.
2. Improved Handling and Transport
- Pellets are easier to handle, store, and transport compared to loose powders, making them ideal for logistics and processing.
3. Efficient Use of Materials
- The compaction process maximizes the use of raw materials, reducing waste and improving cost-efficiency.
4. Customization
- Custom die designs allow for the production of pellets with specific properties, including hardness, porosity, or release characteristics.
5. Scalability
- Powder pellet press dies can be scaled for both small-scale and large-scale production, providing flexibility for various manufacturing needs.
● Challenges and Considerations
1. Wear and Tear
- Continuous use of pellet press dies can lead to wear, particularly when dealing with abrasive powders. Regular maintenance and die material selection are key to prolonging die life.
2. Pressure Control
- Proper pressure application is crucial to ensure that the pellets are compacted to the desired density without over-compressing, which can lead to cracking or deformation.
3. Material Selection
- The choice of die material should align with the powder's properties and the required end product to ensure optimal performance.
4. Cleanliness and Contamination
- For some applications, particularly in pharmaceuticals, cross-contamination between different powders can affect the quality of the pellets. Regular cleaning and die handling procedures are essential.
● Conclusion
The powder pellet press die is an essential tool in industries ranging from battery manufacturing to pharmaceuticals and metal production. By transforming loose powders into compact, uniform pellets, these dies enhance efficiency, reduce waste, and improve the handling and storage of materials. Whether used for high-volume production or specialized applications, the quality and design of the powder pellet press die play a significant role in the overall performance and consistency of the final product.
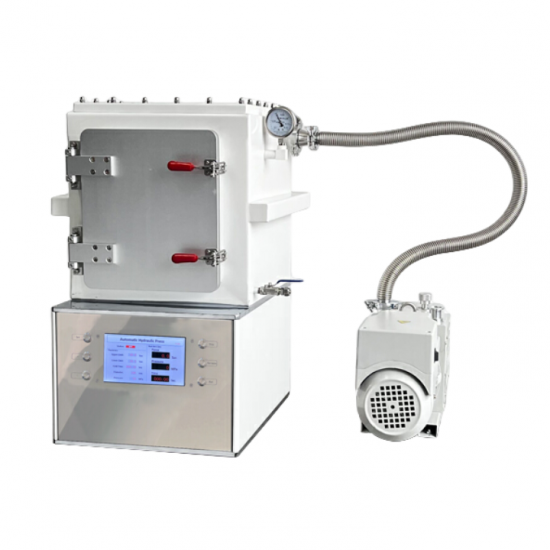