Cold Isostatic Pressing (CIP)
Cold Isostatic Pressing (CIP) is a manufacturing process used to compact powdered materials into solid parts or preforms. This technique leverages uniform pressure applied in all directions to create dense, homogeneous, and high-quality parts without the need for high temperatures. Here's a detailed overview of the process, its applications, advantages, and challenges.
Process of Cold Isostatic Pressing
Equipment and Setup
-
Pressure Vessel: A high-strength container capable of withstanding high pressures, typically made of steel or other robust materials.
-
Elastomeric Mold: A flexible mold, often made of rubber or other elastomeric materials, that holds the powder and conforms to the shape of the final part.
-
Hydraulic Press: A system to generate and apply high-pressure fluid (usually water or oil) uniformly around the mold.
Steps in CIP
-
Powder Preparation: The powder material is prepared, ensuring uniform particle size and distribution. It might be mixed with binders to improve compaction.
-
Mold Filling: The powder is filled into the elastomeric mold. Care is taken to avoid air entrapment and ensure uniform packing.
-
Sealing: The mold is sealed to prevent powder leakage and ensure that the pressure is applied uniformly.
-
Pressurization: The filled mold is placed in the pressure vessel, which is then filled with a fluid. High pressure (up to 400 MPa or more) is applied uniformly in all directions, compacting the powder into a dense form.
-
Depressurization: Once the desired pressure and compaction are achieved, the pressure is slowly released.
-
Part Removal: The compacted part is removed from the mold. It may be ready for use, or it may require further processing such as sintering, machining, or surface treatment.
Applications of Cold Isostatic Pressing
-
Ceramics: Manufacturing dense, high-strength ceramic parts for applications in electronics, medical devices, and aerospace.
-
Metals: Producing preforms for subsequent forging or sintering in industries such as automotive, aerospace, and tooling.
-
Composites: Creating parts from composite powders with improved mechanical properties.
-
Refractories: Forming high-density refractory bricks and components for use in high-temperature environments.
-
Biomedical Implants: Producing porous structures for bone implants and other medical applications.
Advantages of Cold Isostatic Pressing
-
Uniform Density: The isostatic pressure ensures uniform density throughout the part, reducing the risk of defects and improving mechanical properties.
-
Complex Shapes: Capable of producing complex shapes that are difficult to achieve with uniaxial pressing.
-
High Green Strength: The parts produced have high green strength, making them easier to handle before sintering or further processing.
-
Material Efficiency: Minimizes material waste, as the process can utilize nearly all the powder material.
-
Scalability: Suitable for both small-scale and large-scale production, allowing flexibility in manufacturing.
Challenges and Limitations
-
Equipment Cost: High initial investment in pressure vessels, molds, and hydraulic systems.
-
Cycle Time: The process can be time-consuming, especially for large or complex parts, which can impact production rates.
-
Mold Wear: Elastomeric molds can wear out or degrade over time, requiring regular maintenance or replacement.
-
Size Limitations: The size of the pressure vessel limits the maximum size of parts that can be produced.
-
Post-Processing: Parts often require further processing, such as sintering, to achieve the desired final properties, adding to production complexity and cost.
Development Challenges
-
Material Compatibility: Expanding the range of materials that can be effectively processed using CIP, including new alloys and composites.
-
Process Optimization: Improving the efficiency and cycle times of the process to enhance productivity and reduce costs.
-
Automation and Control: Developing advanced control systems to automate the process and ensure consistent quality.
-
Environmental Impact: Reducing the environmental footprint of the process, including minimizing the use of non-recyclable mold materials and optimizing energy usage.
Conclusion
Cold Isostatic Pressing is a versatile and effective method for producing high-density, high-quality parts from powdered materials. While it offers significant advantages in terms of uniformity, complexity, and material efficiency, it also presents challenges such as equipment costs and cycle times. Ongoing research and development are essential to overcome these challenges, improve the process, and expand its applications across various industries.
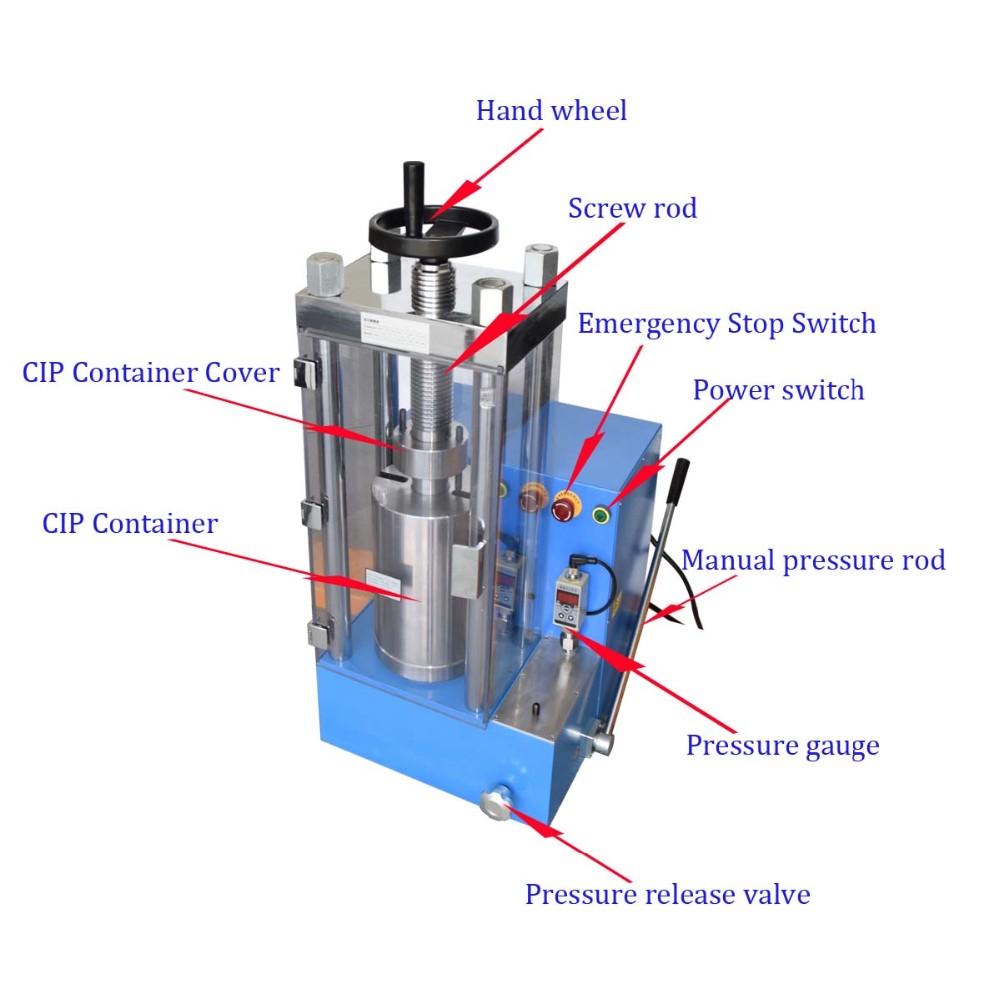